Gate valves are widely utilized in industrial, commercial, and residential applications due to their efficient flow control and tight shut-off capabilities. These valves are particularly favored for their minimal pressure drop when fully open, making them ideal for isolating flow in pipelines. However, like any mechanical component, gate valves are prone to wear and tear, leading to potential issues such as leaks, blockages, or complete failure.
Understanding the proper use, maintenance, and repair of gate valves is crucial for ensuring their longevity and reliable performance. This guide explores the functionality, common issues, troubleshooting methods, and best practices for maintaining gate valves in peak condition.
A gate valve is a linear-motion valve designed to either fully open or fully close the flow of fluid in a pipeline. It operates by moving a gate (which can be a flat, wedge-shaped, or parallel disc) up and down within the valve body. When open, the gate retracts completely, allowing for unobstructed flow with minimal turbulence. When closed, it forms a tight seal against the valve seats, preventing any fluid from passing through.
Unlike globe valves, which are used for throttling, gate valves are strictly for on/off control and are not suitable for regulating flow. Using a gate valve for throttling can lead to premature wear and inefficient operation.
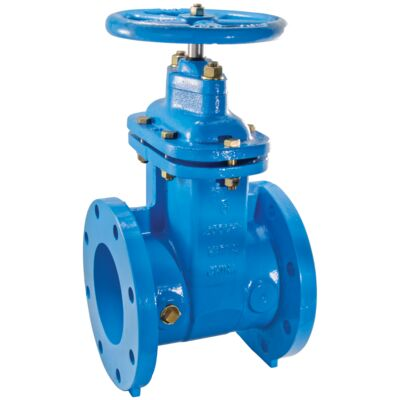
Gate valves come in several types, each suited for different applications:
The stem moves up and down with the gate, providing a visual indication of the valve’s position.
The stem remains in place while the gate moves, making it ideal for confined spaces such as underground installations.
Uses a wedge-shaped gate that tightly presses against the valve seats for enhanced sealing.
Features a flat gate with parallel seats, often used in low-pressure applications.
Designed for slurry, wastewater, and other heavy-duty applications, with a thin, sharp-edged gate to cut through debris.
Gate valves are manufactured using different materials to suit various operating conditions:
Used for water supply, HVAC, and municipal applications.
Stronger than cast iron, making it ideal for wastewater treatment and industrial processes.
Offers excellent corrosion resistance for use in chemical and food processing industries.
Common in plumbing and marine applications due to their resistance to seawater and corrosion.
These valves are employed in diverse industries, including oil and gas, power plants, water treatment facilities, and fire protection systems.
Gate valves are manually or automatically operated using a handwheel, electric actuator, or pneumatic actuator. The primary operating mechanism involves rotating a stem to raise or lower the gate:
Rotating the stem clockwise lowers the gate, closing the valve and stopping fluid flow.
Rotating the stem counterclockwise lifts the gate, allowing fluid to flow freely.
While simple in operation, prolonged exposure to harsh conditions or improper use can lead to functional issues.
Despite their durability, gate valves can develop problems over time. Understanding these issues and implementing effective solutions can extend the valve’s lifespan and prevent costly failures.
Cause:
Accumulation of dirt, sand, or debris in the valve body.
Common in water and slurry pipelines that transport suspended particles.
Symptoms:
Difficulty in fully closing the valve, leading to leakage.
Reduced flow rate even when the valve is open.
Solution:
Periodically flush the pipeline to remove sediment.
If the buildup is severe, disassemble the valve and clean the internal components.
Cause:
Corrosion of internal components due to exposure to aggressive chemicals.
Lack of lubrication on the stem and moving parts.
Thermal expansion causing the gate to seize.
Symptoms:
The valve does not respond to handwheel operation.
Resistance when trying to turn the stem.
Solution:
Isolate the valve by shutting off the fluid supply.
Apply penetrating lubricant to loosen stuck components.
Gently tap the valve body with a mallet to free the gate.
If the issue persists, dismantle the valve and inspect for corrosion or physical damage.
Cause:
Worn-out packing material around the stem.
Loose or damaged gland nuts.
Improper installation leading to misalignment.
Symptoms:
Visible fluid leakage from the stem area.
Reduced sealing performance.
Solution:
Tighten the packing gland bolts to compress the seal.
Replace the packing if it appears worn or degraded.
Ensure correct installation and alignment of components.
When gate valve issues arise, follow these systematic troubleshooting steps:
Determine whether the valve is leaking, jammed, or failing to open/close.
Inspect surrounding pipes for additional factors causing the issue.
Shut off the fluid supply and depressurize the system before attempting repairs.
Ensure safety precautions are in place to prevent spills or injuries.
Remove the valve bonnet and examine the gate, stem, and seats for wear or damage.
Clean accumulated debris and check for corrosion.
Install new packing seals, gaskets, or a replacement gate if necessary.
Lubricate moving parts before reassembly.
Reinstall the bonnet and ensure all fasteners are secure.
Open and close the valve multiple times to verify smooth operation.
Check for leaks after restoring the fluid flow.
Regular maintenance can significantly enhance the performance and longevity of gate valves. Follow these best practices:
Routine Inspection: Periodically check for leaks, corrosion, and operational issues.
Lubrication: Apply grease to the stem and moving parts to prevent seizing.
Cleaning: Flush the pipeline regularly to prevent sediment buildup.
Seal Replacement: Replace worn-out gaskets and packing before they cause major leaks.
Gate valves are critical components in fluid control systems, providing reliable isolation and minimal pressure drop. However, they are susceptible to problems such as sediment accumulation, corrosion, and leakage if not properly maintained.
By understanding common issues, implementing effective troubleshooting techniques, and performing routine maintenance, operators can ensure long-lasting, trouble-free performance from gate valves. Whether in industrial plants, municipal water systems, or oil and gas pipelines, these valves play a vital role in maintaining system efficiency and safety.
Investing time in gate valve maintenance not only prevents costly repairs but also extends the life of the entire pipeline system. With proper care, these valves can provide years of dependable service.
Next: What Is A Safety Valve Used For?
Previous: Hand-Operated Globe Control Valve: Essential for Fluid and Gas Regulation